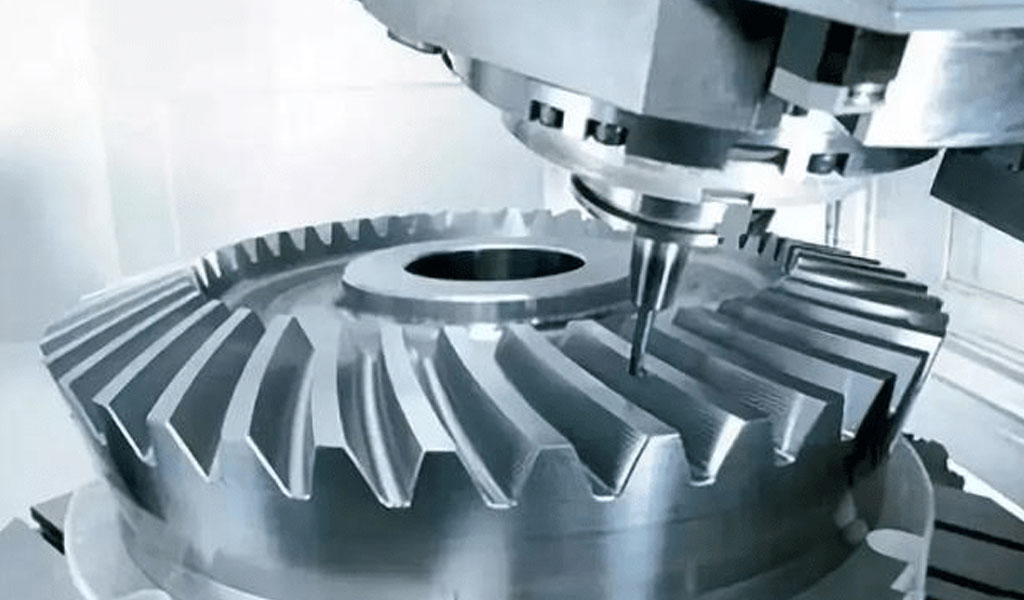
나사 가공은 CNC 가공 센터의 매우 중요한 응용 분야 중 하나입니다. 나사의 가공 품질과 효율성은 부품의 가공 품질과 가공 센터의 생산 효율성에 직접적인 영향을 미칩니다. CNC 가공 의 성능이 발전 하고 절삭 공구가 개선됨에 따라 나사 가공 방법이 지속적으로 개선되고 있으며 나사 가공의 정확도와 효율성이 점차 향상되고 있습니다. 기술자가 가공에서 나사 가공 방법을 합리적으로 선택하고 생산 효율성을 개선하며 품질 사고를 피할 수 있도록 실제로 CNC 가공 센터에서 일반적으로 사용되는 여러 나사 가공 방법을 다음과 같이 요약합니다.
가장 일반적인 방법 – 탭 처리 방법
- 탭가공의 분류 및 특징
탭을 사용하여 나사 구멍을 가공하는 것은 가장 일반적인 가공 방법입니다. 주로 직경이 작고(D<30) 구멍 위치 정확도 요구 사항이 낮은 나사 구멍에 적합합니다.
1980년대에는 나사 구멍이 모두 유연한 태핑 방법을 채택했습니다. 즉, 유연한 태핑 척을 사용하여 탭을 고정했기 때문에 태핑 척을 사용하여 공작 기계의 비동기 공급과 스핀들 속도로 인해 발생하는 진전을 따라잡기 위해 축 보정을 수행할 수 있습니다. 오류를 표시하여 올바른 피치를 확인합니다. 유연한 태핑 척은 구조가 복잡하고 비용이 많이 들고 손상되기 쉽고 가공 효율이 낮습니다. 최근 몇 년 동안 CNC 가공 센터의 성능이 점차 향상되었고 강성 태핑이 CNC 가공 센터의 필수 구성이 되었습니다.
따라서 강성 태핑은 현재 가장 일반적인 나사 가공 방법이 되었습니다. 즉, 탭은 강성 스프링 척으로 클램핑되고 스핀들 이송 및 스핀들 속도는 공작 기계에 의해 제어되어 동일하게 유지됩니다. 유연한 태핑 척과 비교할 때 스프링 척은 구조가 간단하고 가격이 저렴하며 사용 범위가 넓습니다. 탭을 클램핑하는 것 외에도 엔드밀, 드릴 및 기타 도구를 클램핑할 수 있어 도구 비용을 줄일 수 있습니다. 동시에 강성 태핑은 종종 고속 절삭에 사용되어 가공 센터의 효율성을 높이고 제조 비용을 줄입니다.
- 탭핑 전 나사산 바닥 구멍 결정
나사산 바닥 구멍의 가공은 탭의 수명과 나사산 가공의 품질에 큰 영향을 미칩니다. 일반적으로 나사산 바닥 구멍 드릴 비트의 직경은 나사산 바닥 구멍 직경 허용 오차의 상한에 가깝게 선택됩니다.
예를 들어, M8 나사 구멍의 바닥 구멍 직경은 Ф6.7+0.27mm이고 드릴 비트 직경은 Ф6.9mm입니다. 이런 식으로 탭의 가공 여유를 줄이고 탭의 하중을 줄이고 탭의 서비스 수명을 늘릴 수 있습니다.
- 수도꼭지는 어떻게 선택하나요?
탭을 선택할 때는 우선 가공할 소재에 따라 해당 탭을 선택해야 합니다. 도구 회사는 가공할 소재에 따라 다양한 유형의 탭을 생산합니다. 선택에 특히 주의하세요.
밀링 커터와 보링 커터와 비교했을 때 탭은 가공되는 소재에 매우 민감합니다. 예를 들어, 알루미늄 부품을 가공하기 위해 주철을 가공하는 데 탭을 사용하면 나사산 손실, 무작위 좌굴 또는 탭 파손이 발생하여 작업물이 폐기될 수 있습니다. 둘째, 관통 홀 탭과 블라인드 홀 탭의 차이점에 주의하세요. 관통 홀 탭의 앞쪽 끝은 더 길게 안내되고 칩 제거는 앞쪽 칩 제거입니다. 블라인드 홀의 앞쪽 끝은 더 짧고 칩 제거는 뒤쪽입니다. 관통 홀 탭이 있는 블라인드 홀의 경우 나사 가공 깊이를 보장할 수 없습니다. 또한 유연한 태핑 척을 사용하는 경우 탭 섕크의 직경과 정사각형의 너비는 태핑 척의 직경과 같아야 합니다. 강성 태핑의 탭 섕크 직경은 스프링 콜렛의 직경과 같아야 합니다. 간단히 말해, 합리적인 탭 선택만이 정밀 CNC 가공을 보장할 수 있습니다 .
- 탭 가공을 위한 CNC 프로그래밍
탭 가공의 프로그래밍은 비교적 간단합니다. 현재 가공 센터는 일반적으로 탭핑 서브루틴을 굳건히 하고 각 매개변수만 할당하면 됩니다. 그러나 수치 제어 시스템이 다르기 때문에 서브루틴의 형식이 다르고 일부 매개변수의 의미가 다르다는 점에 유의해야 합니다. 예를 들어 SIEMEN840C 제어 시스템의 경우 프로그래밍 형식은 G84 X_Y_R2_ R3_R4_R5_R6_R7_R8_R9_R10_R13_입니다. 프로그래밍하는 동안 이 12개 매개변수만 할당하면 됩니다.
크고 복잡한 구멍 스레드 – 스레드 밀링 방법
- 스레드 밀링의 특징
스레드 밀링은 스레드 밀링 도구, 가공 센터의 3축 연동 장치, 즉 X, Y축 원호 보간, Z축 선형 이송 밀링 방식으로 스레드를 가공합니다.
스레드 밀링은 특히 가공하기 어려운 재료의 큰 구멍 스레드와 나사 구멍 가공에 사용됩니다. 주로 다음과 같은 특징이 있습니다.
- ⑴ 가공 속도가 높고, 효율이 높고, 가공 정밀도가 높다. 공구 재료는 일반적으로 경질 합금 재료이므로 절삭 속도가 빠르다. 공구의 제조 정밀도가 높기 때문에 밀링의 나사 정밀도가 높다.
- ⑵ 밀링공구의 범위가 넓습니다. 피치만 같으면 좌나사든 우나사든 보통 하나의 공구를 사용하는데, 공구의 값을 자르는 데 유용합니다.
- ⑶ CNC 밀링 가공은 칩과 먼지를 제거하기가 간단하므로 절삭 성능이 탭보다 가장 좋습니다. 특히 알루미늄, 구리, 크롬강 및 기타 가공이 어려운 소재의 나사 가공에 적합합니다.이 기계는 대형 부품이나 귀중한 소재의 부품에 대한 나사 가공에 특히 적합하며, 나사 가공의 품질과 그에 따른 작업물의 안전성을 보장할 수 있습니다.
- ⑷ 툴팁 가이드가 없으므로 짧은 나사산 바닥 구멍이 있는 막힌 구멍과 언더컷이 없는 구멍을 가공하는 데 적합합니다.
스레드 밀링 도구의 분류
CNC 밀링 도구는 종종 두 가지 유형으로 나뉩니다. 하나는 기계 고정식 시멘트 카바이드 블레이드 밀링 커터이고 다른 하나는 일체형 시멘트 카바이드 밀링 커터입니다. 기계 고정 도구는 광범위한 응용 분야를 제공합니다. 나사산 깊이가 있지만 블레이드 길이인 구멍이나 블레이드 길이보다 나사산 깊이가 큰 구멍을 가공할 수 있습니다. 일체형 시멘트 카바이드 밀링 커터는 일반적으로 나사산 깊이가 도구 길이보다 작은 구멍을 가공하지 않습니다.
스레드 밀링을 위한 CNC 프로그래밍
스레드 밀링 도구의 프로그래밍은 다른 도구의 프로그래밍과 다릅니다. 가공 프로그램이 잘못 프로그래밍되면 도구 손상이나 스레드 가공 오류가 발생하기 쉽습니다. 컴파일할 때 다음 사항에 집중하세요.
우선, 나사산이 있는 바닥 구멍을 기계로 가공해야 하며, 작은 지름의 구멍은 드릴로 가공해야 하며, 더 큰 구멍은 보링 작업을 통해 나사산이 있는 바닥 구멍의 정확성을 확인해야 합니다.
공구가 절단 인 및 아웃할 때 아크 궤적을 채택해야 하며, 일반적으로 절단 인 또는 아웃을 위해 1/2 원을 사용하므로 Z축 방향은 나사산 모양을 확인하기 위해 1/2 피치를 이동해야 합니다. 이 지점에서 공구 반경 보정 값을 가져와야 합니다.
X, Y축 원호 보간은 한 원이며, 스핀들은 Z축 방향으로 피치를 이동해야 합니다. 그렇지 않으면 무작위 나사산이 발생합니다.
백업 스레드 방식 – 픽앤클릭 방식
픽 방법의 특징
상자 부품에는 큰 나사 구멍이 종종 생기는 경우가 많습니다. 탭과 나사 밀링 커터가 없는 경우 선반에서 픽킹을 하는 것과 비슷한 방법이 종종 사용됩니다.